BEARINGS
Bearings permit smooth, low-friction movement between two or more surfaces. Conventional bearings provide support to rotating machinery by allowing relative movement. They allow rotation and provide support in either radial or axial planes of rotation. The most common types of bearings are rolling element bearings, and oil film or journal bearings. Bearings reduce friction by providing smooth metal balls or rollers. These balls or rollers “bear” the load, allowing the device to spin smoothly
Bearings typically have to deal with two kinds of loading, radial and thrust. Depending on where the bearing is being used, it may see all radial loading, all thrust loading or a combination of both e.g. electric motor bearing supports a radial load , a revolving stool bearing supports axial or thrust load
What is load?
Load is the force applied to the bearing, which the bearing has to withstand. Generally there are two types of load
1) Radial load is the load which is applied perpendicular to the shaft axis.
2) Axial load is the load applied parallel to the shaft axis
3) Combined load is radial plus axial load
Principle of operation
Rolling element bearings consist of a stationary outer race and a rotating inner race; in between them are the rolling elements, most common are spherical balls, but cylinders or tapered pins are also used. During rotation, these 3 items are in contact with each other and the weight being supported is transferred through the rolling elements between the inner race and outer race.
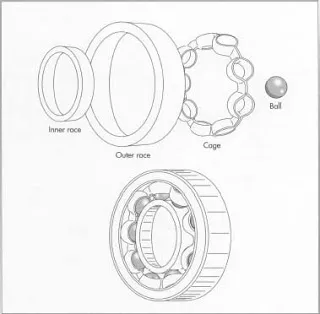
Oil film bearings have no rolling elements, but make use of pressurized oil to provide a film of support, and prevent galling between the shaft and the bearing journal. The oil is circulated so that fresh, cool oil is constantly entering the space between the stationary and rotating pieces. The shaft rotation shears the oil in this gap, causing it to heat up. The oil then exits the journal for cooling, filtering, and recirculation.
Types of bearings
1) Ball bearings
Ball bearings are very commonly used. They are found in everything from skate boards, to washing machines to PC hard drives. These bearings are capable of taking both radial and thrust loads, and are usually found in applications where the load is light to medium and is constant in nature (i.e. not shock loading). In a ball bearing, the load is transmitted from the outer race to the ball and from the ball to the inner race
2) Roller bearings
Roller bearings are used in heavy duty applications such
as conveyor belt rollers, where they must hold heavy radial loads. In these bearings the roller is a cylinder, so the contact between the inner and outer race is not a point (like the ball bearing above) but a line. This spreads the load out over a larger area, allowing the roller bearing to handle much greater loads than a ball bearing. However, this type of bearing cannot handle thrust loads to any significant degree. A variation of this bearing design is called the needle bearing. The needle roller bearing uses cylindrical rollers but with a very small diameter. This allows the bearing to fit into tight places such as gear boxes that rotate at higher speeds.
Ball thrust bearings are mostly used for low-speed non precision applications. They cannot take much radial load.
Roller thrust bearings can support very large thrust loads. They are often found in gearsets like car transmissions between gears
5) Taper roller bearing
Tapered roller bearings are designed to support large radial and large thrust loads. These loads can take the form of constant loads or shock loads. Tapered roller bearings are used in many car hubs, where they are usually mounted in pairs facing opposite directions. This gives them the ability to take thrust loads in both directions.
6) Magnetic Bearing
Magnetic bearing systems represent a completely different approach to the support of rotating equipment. Magnetic bearings are a non-contact technology, which means negligible friction loss and no wear, and higher reliability. It also enables previously unachievable surface speeds to be attained. Lubrication is eliminated, meaning that these bearings can be incorporated into processes that are sensitive to contamination, such as the vacuum chambers in which many semiconductor manufacturing processes take place.
General Application Guidelines:
Ball bearings are the less expensive choice in the smaller sizes and under lighter loads, while roller bearings are less expensive for larger sizes and heavier loads. Roller bearings are more satisfactory under shock or impact loading than ball bearings. Ball-thrust bearings are for pure thrust loading only. At high speeds, a deep-groove or angular-contact ball bearing usually will be a better choice, even for pure thrust loads. Self-aligning ball bearings and cylindrical roller bearings have very low friction coefficients. Deep-groove ball bearings are available with seals built into the bearing so that the bearing can be pre-lubricated to operate for long periods reducing maintenance requirements.
Rolling bearing types
Numerous rolling bearing types with standardized main dimensions are available for the various requirements. Rolling bearings are differentiated according to: – (1) the direction of main load: radial bearings and thrust bearings. Radial bearings have a nominal contact angle a0 of 0° to 45°. Thrust bearings have a nominal contact angle a0 of over 45° to 90°. – (2) The type of rolling elements: ball bearings and roller bearings.
Difference between Ball & Roller bearing
The essential differences between ball bearings and roller bearings are,
– Ball bearings: lower load carrying capacity, higher speeds
– Roller bearings: higher load carrying capacity, lower speeds
Rolling bearing components
Rolling bearings generally consist of bearing rings (inner ring and outer ring), rolling elements which roll on the raceways of the rings, and a cage which surrounds the rolling elements. The lubricant also has to be regarded as a rolling bearing component as a bearing can hardly operate without a lubricant. Seals are also increasingly being integrated into the bearings.
Types of Rolling elements
Rolling elements are classified, according to their shape, into balls, cylindrical rollers, needle rollers, tapered rollers and barrel rollers. The rolling elements function is to transmit the force acting on the bearing from one ring to the other. For a high load carrying capacity it is important that as many rolling elements as possible, which are as large as possible, are accommodated between the bearing rings. Their number and size depend on the cross section of the bearing. Also it is just as important for loadability that the rolling elements within the bearing are of identical size.
Comments are closed.