1. Waterline corrosion or Concentration cell corrosion
This type of corrosion occurs due to electrochemical attack of the metal surface exposed to electrolyte of varying concentrations or varying aeration.
This type of corrosion is due to
(i) Difference in concentration of metal ions.
(ii) Difference in the exposure to air/oxygen (Differential aeration corrosion)
(iii) Difference in temperature.
· Differential aeration corrosion is the most common type of concentration cell corrosion. When a metal is exposed to different air concentrations, it has been found to be poorly oxygenated of the metal becomes anodic and well oxygenated part becomes cathodic.
· The potential difference is created which causes the flow of electrons from anode (metallic part immersed in NaCl solution) to cathode (exposed to atmosphere).
Eg. Zn rod immersed deep in NaCl solution: Anode
Zn rod above NaCl solution: Cathode
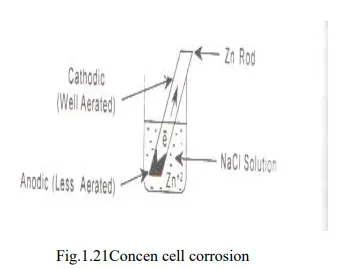
Crevice corrosion
Crevice corrosion refers to corrosion occurring in confined spaces to which the access of the working fluid from the environment these spaces are generally called crevices. Examples of crevices are gaps and contact areas between parts, under gaskets or seals, inside cracks and seams, spaces filled with deposits and under sludge piles.
Crevice corrosion usually occurs in gaps a few micrometers wide, and is not found in grooves or slots in which circulation of the corrodent is possible. Crevice corrosion is a very similar mechanism to corrosion. Crevice corrosion can be viewed as a less severe form of localized corrosion when compared with pitting. The depth of penetration and the rate of propagation in pitting corrosion are significantly greater than in crevice corrosion.
Factors effecting corrosion
The rate and extent of corrosion depends upon various factors due to nature of metal and nature of corroding environment.
Factors due to nature of metal
1. Purity of the metal: Heterogeneity of the metal is due to the presence of impurities which form tiny electrochemical cells at the exposed parts. The anodic parts get corroded.
2. Electrode potentials: metals with higher reduction potentials do not corrode easily. They are noble metals like gold, platinum and silver. Whereas the metals with lower reduction potentials readily undergo corrosion (eg. Zn, Mg, Al etc.).
3. Position of metal in galvanic series: Metals which possess low reduction potentials and occupy higher end of galvanic series undergo corrosion easily.
4. Metals which possess high reduction potentials and occupy lower end of galvanic series do not undergo corrosion and they get protected.
· When two metals are in electrical contact in presence of an electrolyte, then the metal which is more active undergoes corrosion.
· The rate of corrosion depends on the difference in their position in Galvanic series. Greater the difference more will be the extent of corrosion at anode.
Eg. The potential difference between Fe and Cu is 0.78V which is more than that between Fe and Sn (0.30V). Therefore, Fe corrodes faster when in contact with Cu than that with Sn. on this account, the use of dissimilar metals should be avoided wherever possible (Eg. Bolt & nuts, screw & washer).
4. Relative areas of anodic and cathodic cells: the relative areas o of corrosion is influenced by cathodic to anodic cells.
5. If the metal has small anodic and large cathodic area, the rate of corrosion is very high. This is because the electrons are liberated at anode which is consumed at cathode. If the cathodic area is larger, the liberated electrons are rapidly consumed at cathode. This further enhances the anodic reaction leading to increase the rate of corrosion.
6. Hydrogen over voltage: when a cathode reaction is hydrogen evolution type, the metal with Lower hydrogen over voltage on its surface is more susceptible for corrosion, since the liberation of hydrogen gas is easy at this condition. Hence the cathodic reaction is very fast which in turn Makes anodic reaction fast. Hence the rate of corrosion increases. Higher the over voltage, lesser is the corrosion.
7. Physical state of metal: Metals with small grain size have more tendencies to undergo corrosion. Metal with more stress/strain also undergoes corrosion easily.
8. Nature of surface film: If the corrosion product formed is more stable, insoluble and nonporous, it acts as protective layer and prevents further corrosion (Eg. Ti, Al and Cr). If the corrosion product is porous, volatile and soluble, it further enhances the corrosion (Fe, Zn and Mg).
Factors due to nature corrosive environment
1. Temperature: the rate of corrosion reactions increases with increase in temperature.
2. Humidity in air: the moisture or humidity present in atmosphere furnishes water to the electrolyte which is essential for setting up of an electrochemical cell. The oxide film formed has the tendency to absorb moisture which creates another electrochemical cell.
3. Presence of impurities: Atmosphere is contaminated with gases like CO2, SO2, H2S; fumes of H2SO4, HCl etc. and other suspended particles in the vicinity of industrial areas. They are Responsible for electrical conductivity, thereby increasing corrosion.
4. P H value: pH value of the medium has the greater effect on corrosion. Acidic pH increases the rate of corrosion.
5. Amount of oxygen in atmosphere: As the percentage of oxygen in atmosphere increases, the rate of corrosion also increases due to the formation of oxygen concentration cell. The decay of metal occurs at the anodic part and the cathodic part of the metal is protected.
Comments are closed.