Single Piece or Solid Pattern
In a simple solid pattern, one side is made flat which serves as a parting surface. In this case, the
mold cavity will be entirely in the drag, and requires the more number of manual operations such
as cutting the gating system and repairing of the mold. The shape of the single piece pattern is
exactly same as that of casting. Single piece patterns are inexpensive and best suited for limited
production.
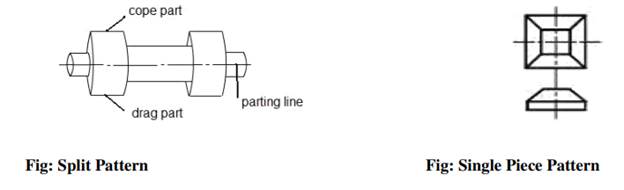
Split Pattern
Split pattern is made in two parts. One part producing the mold in drag and the other in cope.
They are kept in position by dowel pins, and the split is usually arranged along the parting line to
draw the pattern easily out of the mold before pouring of molten metal. Split piece patterns are
used for intricate castings or castings of unusual shapes.
Multi Piece Pattern
Pattern with three or more parts is used for more complex castings. This type of pattern is known
as multi piece pattern. It requires molding box with three parts. The middle one is called cheek.
Loose Piece Pattern
Loose piece pattern is used to produce the castings having projections in the sides. Such design
makes impossible to draw the pattern from the mold. It is therefore necessary to make such
projection in loose piece and fastened to main pattern by means of anchor pin.
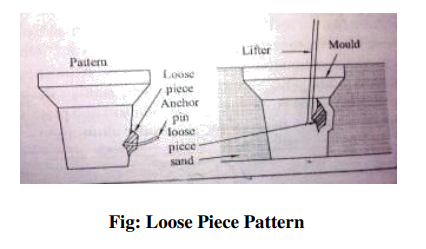
Match Plate Pattern
In this case, pattern in two halves is attached on opposite side of wooden or metal plate (match plate). Production efficiency and dimensional accuracy of castings can be generally improved by the use of these patterns. Several patterns for small castings (need not be same) can be mounted on one match plate. These are mostly used in machine molding as well as for producing large number of small castings by hand molding.
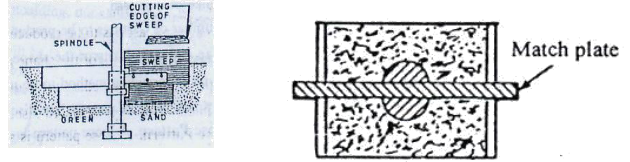
Fig: Sweep Pattern Fig: Match Plate Pattern
Sweep Pattern
It is not a true pattern, but a template made of wood or metal revolving around a fixed axis in the
mold shapes the sand to the desired contour. This eliminates the need for a large three
dimensional pattern. It is suitable for producing simple symmetrical castings such as wheels,
rims, and bell shapes.
Runner
Runner is a horizontal channel that receives molten metal from the sprue base, and distributes to the ingates which carries metal to the mold. Runners are usually made trapezoidal in cross section. They are generally located in cope and ingates in the drag. This ensures that the slag and dross are trapped in the upper portion of runner and only molten metal enters into the mold.
Runner Extension
The runner is often extended beyond the last ingate to retain inclusions and various refractory
materials that may have been washed along the stream of molten metal. Also, it absorbs kinetic
energy causing a smooth flow of metal into the mold cavity.
Gates or Ingates
Gates or ingates are openings through which molten metal directly enters into the mold cavity.
The gates should be designed such that the molten metal can flow steadily and quietly into the
mold cavity. They should be easily removed from the casting after solidification.
Tools and Equipment
Molding Board
A molding board is a smooth wooden board on which the flask and pattern are placed when the
mould is being made. The figure is shown below:
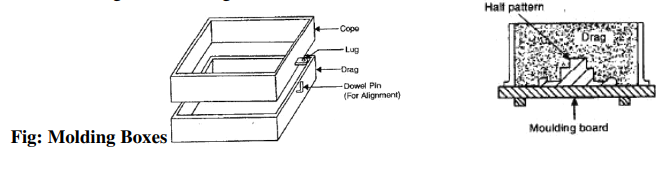
Molding Boxes
Sand moulds are prepared in specially constructed boxes called flasks. The purpose of flask is to
impart the necessary rigidity and strength to the sand in molding. They are usually made in two
parts, held in alignment by dowel pins. The top part is called the cope and the lower part the
drag. These flasks can be made by wood or metal depending upon the size required and the
purpose the flask must serve.
Shovel
A shovel is used for mixing and tempering molding sand and for moving the sand from the pile
to the flask as shown in figure below:
Riddle
A riddle sometimes called a screen consists of a circular or square wooden frame fitted with a
standard wire mesh at the bottom as shown in figure below. It is used to remove coarse sand
particles and other foreign material from the foundry sand.

Rammer
A hand rammer is used for packaging or ramming the sand into the mould. One of its ends,
called the peen end, is wedge shaped and is used for packing sand in spaces, pockets and corners,
in the early stages of ramming. The other end called the butt end, has a flat surface and is used
for compacting the sand towards the end of molding as shown in below figure.
Strike Edge or Strike-Off Bar
It is a piece of metal or wood with straight edge as shown in below figure. It is used to remove
excess sand from the mould after ramming, to provide a level surface
Riser Pin
It is a straight wooden pin used to make a hole in the cope over the mold cavity for the molten
metal to rise-in and feed the casting to compensate the shrinkage that may take place during
solidification.
Sprue Pin
It is a tapered wooden pin, as shown in below figure. It is used to make a hole in the cope
through which the molten metal is poured into the mould.

Fig: Sprue Pin Fig: Slick
Slick
It is a small double ended tool having a flat on one end and a spoon on the other end as shown in
below figure. Slicks are used for repairing and finishing small surfaces of the mould.
Lifter
Lifters are made of thin sections of steel of various widths and lengths with one end bent at right
angles as shown in below figure. They are used to clean and finish the bottom and sides of deep,
narrow openings in moulds.
Gate Cutter
It is a small piece of tin plate shape as shown in below figure. This serves as a tool for cutting
gates and runners in the mould.
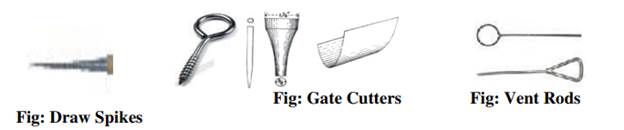
Vent Rod
A vent rod or wire, as shown in below figure is used to make a series of small holes to permit
gases to escape while the molten in being poured.
Drawspike or Screw
The draw spike is appointed steel rod, with a loop at one end. It is used to rap a draw patterns
from the sand. Below figure shows two kinds of draw spikes. The draw spike is threaded on the
end to engage metal patterns.
Comments are closed.