We can alter the characteristics of steel in various ways. In the first place, steel which contains very little carbon will be milder than steel which contains a higher percentage of carbon, up to the limit of about 1 %. Secondly, we can heat the steel above a certain critical temperature, and then allow it to cool at different rates. At this critical temperature, changes begin to take place in the molecular structure of the metal. In the process known as annealing, we heat the steel above the critical temperatureand permit it to cool very slowly. This causes the metal to become softer than before, and much easier to machine. Annealing has a second advantage. It helps to relieve any internal stresses which exist in the metal. These stresses are liable to occur through hammering or working the metal, or through rapid cooling. Metal which we cause to cool rapidly contracts more rapidly on the outside than on the inside. This produces unequal contractions, which may give rise to distortion or cracking. Metal which cools slowly is less liable to have these internal stresses than metal which cools quickly.
On the other hand, we can make steel harder by rapid cooling. We heat it up beyond the critical temperature, and then quench it in water or some other liquid. The rapid temperature drop fixes the structural change in the steel which occurred at the critical temperature, and makes it very hard. But a bar of this hardened steel is more liable to fracture than normal steel. We therefore heat it again to a temperature below the critical temperature, and cool it slowly. This treatment is called tempering. It helps to relieve the internal stresses, and makes the steel less brittle than before. The properties of tempered steel enable us to use it in the manufacture of tools which need a fairly hard steel. High carbon steel is harder than tempered steel, but it is much more difficult to work.
These heat treatments take place during the various shaping operations. We can obtain barsand sheets of steel by rolling the metal through huge rolls in a rolling-mill. The roll pressures must be much greater for cold rolling than for hot rolling, but cold rolling enables the operators to produce rolls of great accuracy and uniformity, and with a better surface finish. Other shaping operations include drawing into wire, casting in moulds, and forging.
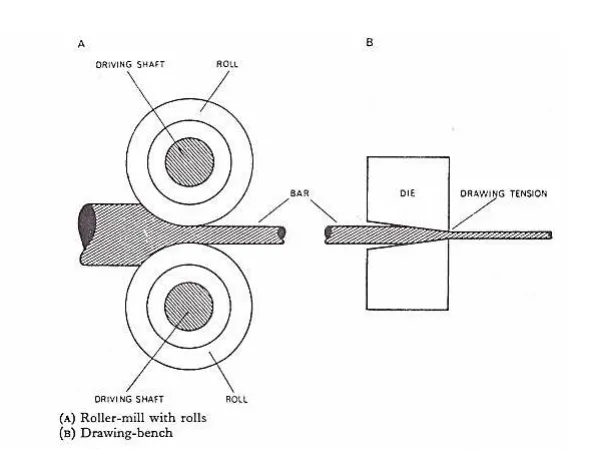
Comments are closed.