Plastic is a substance that can be easily formed or moulded into a desired shape.
Plastic can be formed in a desired shape by the effect of mechanical force & heat.
In the manufacture of plastic raw materials like coal, petroleum, cellulose, salt, sulphur, limestone, air, water etc are used.
Plastics as engineering materials:-
Advantages of plastics over other engineering materials.
(1) Low fabrication cost, low thermal & electrical conductivities, high resistance to corrosion & solvents.
(2) The stress – strain relationship of plastics is similar to that of the metals. (
3) Plastics reduce noise & vibration in machines
(4) Plastics are bad conductors of heat are useful for making handles used for hot objects, most plastics are inflammable.
(5) Plastics are electrical insulators & find large scale use in the electrical industry.
(6) Plastics are resistance to chemicals.
(7) Plastics are clear & transparent so they can be given beautiful colours.
Types of Plastic: –
(1) Thermoplastics
(2)Thermosetting plastics.
Difference between thermoplastic & thermosetting resins:-
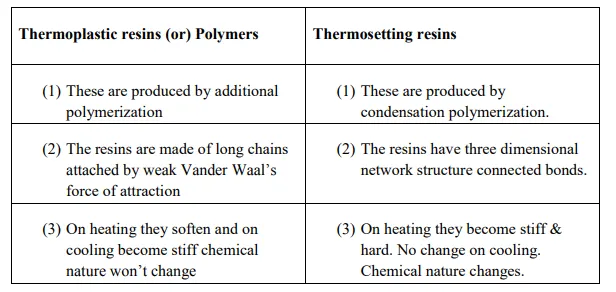
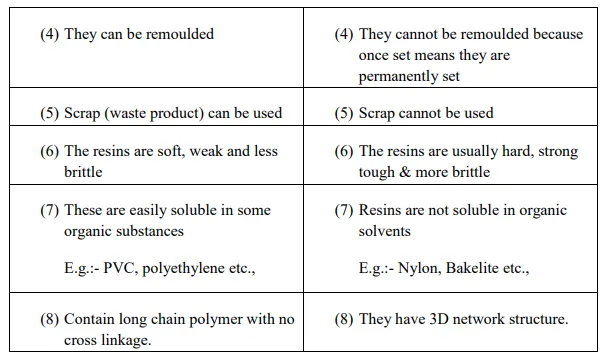
Compounding of plastics:-
Compounding of plastics:- Compounding of plastics may be defined as the mixing of different materials like plasticizers, fillers of extenders, lubricants, pigments to the thermoplastic & thermosetting resins to increase their useful properties like strength, toughness, etc.
Resins have plasticity or binding property, but need other ingredients to be mixed with them for fabrication into useful shapes. Ingredients used in compounding o plastics are (1)Resins (2) Plasticizers (3) fillers (4) pigments (5) Stabilizers.
(1) Resins:- The product of polymerization is called resins and this forms the major portion of the body of plastics. It is the binder, which holds the different constituents together. Thermosetting resins are usually, supplied as linear – polymers of comparatively low molecular weight, because at this stage they are fusible and hence, mouldable. The conversion of this fusible form into cross-linked infusible form takes place, during moulding itself, in presence of catalysts etc.
(2) Plasticizers: – Plasticizers are substances added to enhance the plasticity of the material and to reduce the cracking on the surface.
Plasticizers are added to the plastics to increase the flexibility & toughness. Plasticizers also increase the flow property of the plastics.
e.g.:- Tricresyl phosphate, Dibutyle oxalate, castor oil
(3) Fillers (or) extenders:- Fillers are generally added to thermosetting plastics to increase elasticity and crack resistance. Fillers improve thermal stability, strength, non combustibility, water resistance, electrical insulation properties & external appearance.
E.g.:- Mica, cotton, carbon black, graphite, BaSO4 etc.
(4) Dyes and pigments:- These are added to impart the desired colour to the plastics and give decorative effect.
e.g.:- Lead chromate (yellow), ferro cyanide (blue)
(5) Stabilizers:- Stabilizers are used to improve the thermal stability of plastics,
e.g.:- PVC. At moulding temperature, PVC undergoes decomposition & decolourisation. So during their moulding, stabilizers are used. E.g.:- white lead, head chromate.
Comments are closed.